Coatings with parylene
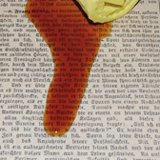
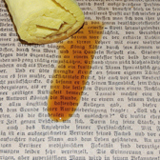
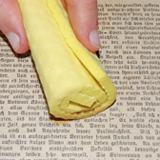
Poly(para-xylylene), or parylene for short, is produced by a CVD process*. Layers of some 100 nm to some 10 µm can be produced. They are characterized by a combination of positive application properties.
The layers:
- have good mechanical properties
- very good dielectric properties
- a gliding surface
- are FDA certified and biocompatible**
- transparent (depending on the layer thickness)
- temperature stable
- chemically inert and solvent resistant
- offer excellent corrosion protection
- represent an excellent permeation barrier
The Parylene*** coating is generally free of tiny holes (pinholes), even in very thin layers. The coating conforms to the surface to a high degree, as the process is characterized by an excellent splitting action, i.e. even places that are difficult to access (e.g. inner surfaces of tubes) can be coated. Porous substrates such as paper and membranes can also be coated.
A wide variety of substrate materials can be coated with parylene: from metals, plastics and elastomers to objects such as plants, insects or archaeological artifacts.
The coating process takes place in a vacuum. In contrast to many other coating processes, the substrate surface is not exposed to elevated temperatures, radiation or solvents. Therefore, even quite sensitive substrates can be coated.
Of particular interest are chemically functionalized parylenes. Currently, amino-functionalized parylenes are available. The amino groups can then be converted in a wet-chemical process, e.g. by bioactive substances. In this way, e.g. implantable stents have been modified for better biocompatibility.
*CVD: Chemical Vapor Deposition
**Classification as "class VI polymer" by USP (United States Pharmacopeia): among other things also implantation test passed
***The spelling "Parylene" (sing.) is also common in the German language